- posted on
Molded Pulp Packaging: The Ultimate Guide (2025 Edition)
Everything brands, packaging buyers, and sustainability managers need to know.
What is Molded Pulp Packaging?
✅ Summary: Molded pulp packaging is eco-friendly, highly customizable, and ideal for protective or retail packaging.
Molded pulp (AKA molded fiber OR paper pulp) is a sustainable, cost-effective alternative to plastic. It can be made from natural fibers, cardboard, or recycled papers and is then formed into custom shapes—like trays, clamshells, protective insert, and even boxes—using heat and pressure. Molded pulp is biodegradable, compostable, and often recyclable, making it a top choice for eco-conscious brands.
For an overview of our molded pulp capabilities, please visit our Molded Pulp Packaging page.
Key Benefits of Molded Pulp Packaging
🌱 Eco-Friendly: Biodegradable and compostable, reducing landfill waste and keeping our oceans clean!
🔒 Protective: Excellent shock absorption for shipping and storage, think egg cartons but prettier!
♻️ Sustainable: Can use post-consumer recycled content!
🎯 Custom-Tailored: Can be formed into all sorts of shapes!
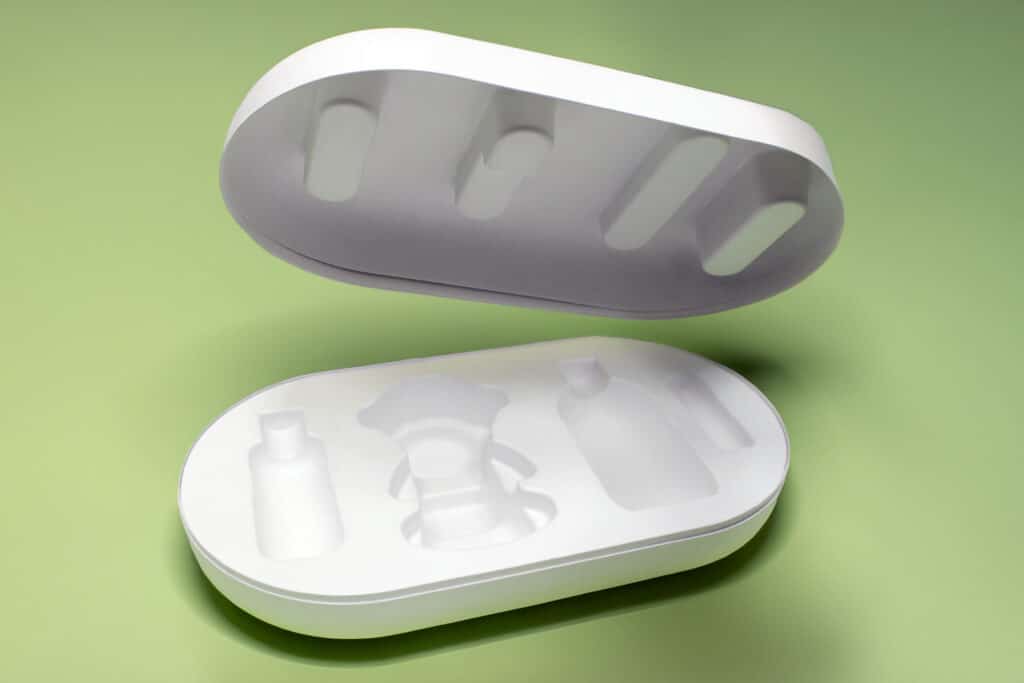
How Molded Pulp Packaging is Made (In a Nutshell)
Molded pulp packaging is produced using one of two main methods: wet-press or dry-press. While the cycle time and forming process may vary, both methods follow a similar core process that includes forming, pressing, trimming/finishing. Each step of this three-part process requires a separate mold (tooling) to complete.
1. Forming
The pulp slurry is shaped inside a custom mold to create the desired packaging form. This is the initial stage in both wet press and dry press molded pulp manufacturing.
1a. Drying (Dry Press Only)
In dry-press molded pulp, the formed packaging is left to air-dry, allowing moisture to evaporate naturally.
2. Pressing
The formed shape is compressed within a heated pressing mold. This step removes excess moisture and enhances surface smoothness and dimensional precision.
3. Trimming or Finishing
Once dried or pressed, molded pulp packaging is trimmed to remove excess material. Optional decorative or functional finishes—such as hot foil stamping, embossing, or pad printing—may be applied to enhance branding or performance.
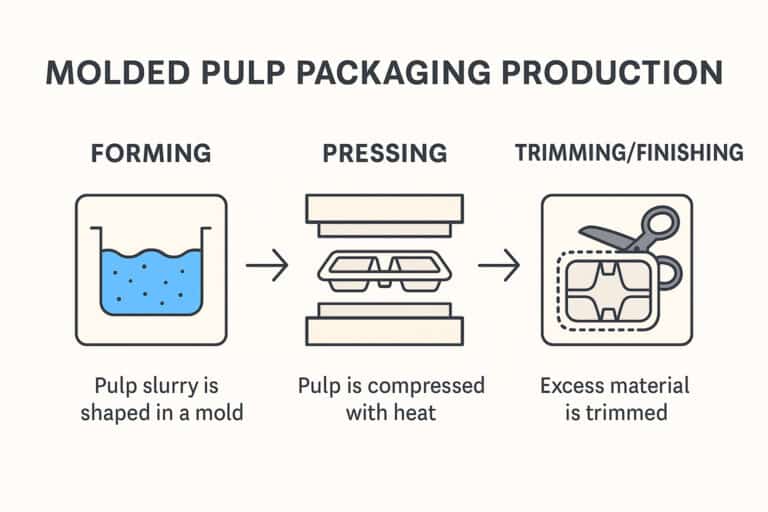
Types of Molded Packaging
There are different ways to classify the types of molded pulp packaging, depending on manufacturing method or industry use. For example, the International Molded Fiber Association (IMFA) outlines molded pulp types such as thick wall, transfer molded, thermoformed, and processed pulp. At Fenix Industries, we simplify this by grouping molded pulp into two main manufacturing categories as previously discussed: wet press and dry press. Wet press molded pulp produces a smooth, premium finish ideal for retail packaging, while dry press is more industrial, faster to produce, and suited for items like trays and protective inserts where function is more important than form. Understanding these types helps brands choose the right molded pulp solution for their product and sustainability goals.
Here’s a breakdown of the primary categories:
1. Dry Press Molded Pulp
- Formed using heated molds after much of the moisture has evaporated from initial forming stage
- Typically coarser texture and thicker walls
- More cost-effective pricing and less expensive tooling
- Slower cycle time due to air-drying process
- Thickness: 1.5mm – 3mm
2. Wet Press Molded Pulp
- Formed and then compressed in heated molds while still wet for a smooth, dense finish
- Premium aesthetic, ideal for consumer-facing products like cosmetics or electronics
- Higher tooling precision, cycle time limited by heat-pressing (anywhere from 2 minutes to 4 minutes per cycle)
- Thickness: 0.7mm – 1mm
IMFA Type 1 - Thick Wall
- Primarily used for support packaging of non-fragile, heavier items (vehicle parts, furniture, etc.) as well as, plant, floral, and nursery pots and containers
- Manufactured using a single mold (tooling)
- Thickness: 5 – 10mm
IMFA Type 2 - Transfer Molded
- Commonly used in egg cartons and trays
- Manufactured using a forming mold and a transfer mold
- Thickness: 3 – 5mm
IMFA Type 3 - Thermoformed Thin Wall
- Closely resembles thermoformed plastic material and may be used as a substitute for thermoformed products (e.g. inserts and tableware)
- Manufactured using multiple heated molds, equivalent to Fenix Industries wet press molded pulp
- Thickness: 2 – 4mm
IMFA Type 4 - Processed
- Can be any of types 1 – 3 but further processed with value-added techniques, most commonly derived from types 2 and 3
- Examples of value-added processes include: coloured pulp, embossing/de-bossing, hot foil stamping, laser engraving
Why More Brands are Switching to Molded Pulp in 2025
Brands are switching to molded pulp packaging because it’s sustainable, protective, and now highly customizable. As manufacturing technology advances, molded pulp can deliver retail-quality finishes while meeting the rising demand for plastic-free solutions. With global leaders like Apple and Sony adopting it, molded pulp is becoming the new standard for eco-friendly, high-performance packaging. Fenix Industries helps brands make this shift with in-house design, engineering support, and full-scale production facilities across the Asia-Pacific region.
🌍 Sustainability Mandates: Governments and retailers demanding plastic reduction
🧾 ESG Reporting: Brands need packaging that aligns with carbon reduction goals
👥 Consumer Demand: Shoppers prefer brands with visible sustainability efforts
🛠️ Improved Technology: Manufacturing processes for molded pulp have matured significantly, allowing for more precise, scalable, and aesthetically pleasing results than ever before
🏢 Adoption by Global Brands: Industry leaders like Sony, Dior, and Chanel are making the switch to molded pulp, setting a precedent for the rest of the market

Image source: Sony Design – Open Box Molding Project
FAQs About Molded Pulp Packaging
Is molded pulp packaging recyclable?
Yes indeed! Most molded pulp packaging can be recycled together with paper waste, but make sure it doesn’t have excessive decoration applied directly to the packaging.
Is molded pulp packaging biodegradable?
Is molded pulp packaging water-resistant or waterproof?
Molded pulp packaging can be made to be water-resistant with additives like AKD (a water-based additive) while still maintaining the recyclability, but waterproofing is still a hurdle yet to be overcome with molded pulp packaging in 2025.
Can I add branding or color directly to molded pulp packaging?
Yes! Many of the traditional printing techniques used in paperboard packaging can also be used for molded pulp. This includes hot foil stamping, silkscreen printing, pad printing, laser engraving, etc.
What is the difference between wet press and dry press molded pulp packaging?
The main difference between wet press and dry press is the manufacturing method, it is also visually different in that wet press molded pulp has a much more refined visual appeal. However, dry press molded pulp is typically less expensive to produce.
How long does it take to produce molded pulp packaging?
This highly depends on the complexity of your project as well as different factors such as if you have design files ready. However, sample tooling typically takes about 10 – 15 days, while production tooling takes around 12 – 20 days.
Can molded pulp really replace plastic packaging?
There are many areas where molded pulp excels in, and with manufacturing improving year on year, the main barrier to entry (pricing) has lowered significantly. Many industries are already able to incorporate molded pulp packaging, but there are still areas where plastics excel in, particularly in the medical field and items that require long term shelf-stability.
Start Your Sustainable Packaging Journey with Fenix Industries
At Fenix Industries, we specialize in high-performance, eco-conscious molded pulp packaging. Whether you’re launching a new product or transitioning away from plastic, we help you design and deliver custom packaging solutions that stand out on shelves—and support your sustainability goals. Our team of packaging industry veterans are ready to help you take your brand to the next level in sustainability!
👉 Let’s work together. Contact us today to get started with a custom molded pulp solution.